Сталь благодаря высокой механической прочности и пластичности
является высококачественным материалом для изготовления ответственных
деталей арматуры. Пластичность стали способствует выравниванию
напряжений в отдельных точках детали и уменьшает опасность ее
внезапного разрушения, что особенно важно для арматуры высоких
параметров и другой ответственной арматуры.
Углеродистые стали.
Углеродистая сталь обыкновенного качества изготовляется по ГОСТ 380—71
(на бессемеровскую сталь не распространяется), качественная,
выплавляемая в основных конверторах, мартеновских и электрических
печах, — по ГОСТ 1050—60.
Углеродистая сталь обыкновенного
качества подразделяется на три группы: А, Б и В. Стали группы А
изготовляются с гарантированными механическими характеристиками после
горячей прокатки; группы Б — с гарантированным химическим составом;
группы В — с гарантированным комплексом механических характеристик и
химического состава. Стали группы А применяются для неответственных
деталей, а для более нагруженных деталей применяются стали групп Б или
В. Стали группы А распространены значительно больше, чем стали групп Б
и В. Сталь каждой группы подразделяется на категории в зависимости от
нормируемых показателей: группа А — 1; 2; ;3; группа Б — 1;
2; группа В — 1; 2; 3; 4; 5; 6. Углеродистые стали могут применяться
при низких температурах: спокойная— до —40° С, кипящая — до —30° С. С
повышением температуры свыше 300° С механические свойства углеродистой
стали быстро снижаются, поэтому сталь обыкновенного качества
применяется до 425° С, качественная — до 455° С.
1.21. Марки углеродистой стали обыкновенного качества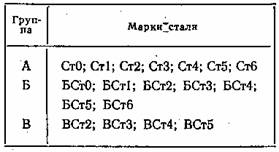
Марки стали приведены в табл. 1.21. В обозначении марок стали буквы
Ст обозначают сталь, цифры от 0 до 6 — условный номер марки, буквы Б и
В обозначают группы. Номер категории ставится в конце обозначения,
первая категория и группа А в обозначении не указываются. Сталь всех
групп с номерами марок 1—4 по степени раскисления изготовляют кипящей
(кп), полуспокойной (пс) и спокойной (сп). Стали с номерами марок 5 и 6
изготовляют полуспокойной и спокойной. Стали марок СтО и БСтО по
степени раскисления не подразделяются. Для соединения сваркой
применяются стали с содержанием углерода менее 0,22%. Если степень
раскисления стали не указывается, номер категории в обозначении
отделяют знаком тире (например, СтЗ—2). Полуспокойная сталь с
повышенным содержанием марганца имеет в обозначении букву Г (например,
ВСтЗГпс).
В табл. 1.22 приведены механические характеристики
углеродистых сталей обыкновенного качества, в табл. 1.23 — цвета
маркировки стали несмываемой краской (независимо от группы и степени
раскисления).
Углеродистая качественная конструкционная сталь по
ГОСТ 1050—60 изготовляется в виде проката и поковок; подразделяется на
две группы: с нормальным (группа I) и повышенным (группа II)
содержанием марганца. Образцы выпускаемой стали подвергаются
механическим испытаниям. Механические характеристики качественной
углеродистой конструкционной стали приведены в табл. 1.24. В
обозначении марки двузначное число указывает среднее содержание
углерода в сотых долях процента, буквы кп — кипящую сталь, Г
(указывается для сталей группы II) — повышенное содержание марганца.
Цвета маркировки качественной стали приведены в табл. 1.25.
Поковки
изготовляются в соответствии с ГОСТ 8479—70, который распространяется
на поковки из конструкционной и легированной сталей, изготовляемые
методом свободной ковки и горячей штамповки.
1.22. Механические характеристики горячекатаной углеродистой стали обыкновенного качества (по ГОСТ 380—71)
1.23. Цвета маркировки т углеродистых сталей обыкновенного качества (по ГОСТ 380—71)
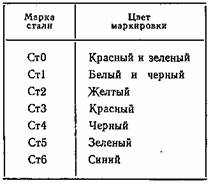
В зависимости от объема и методов контроля механических свойств и
условий комплектования партии поковки подразделяются на пять групп:
1) группа I — испытания механических свойств не производятся, поковки изготовляются из стали одной марки;
2) группа II—определяется твердость НВ образцов от партии, поковки изготовляются из стали одной марки и совместно подвергаются термической обработке;
3) группа III — определяется твердость НВ каждой поковки, поковки изготовляются из стали одной марки и подвергаются термической обработке по одному режиму;
4) группа IV — определяется твердость НВ каждой поковки и механические характеристики

образцов от партии; поковки изготовляются из металла одной плавки и совместно подвергаются термической обработке;
5) группа V — определяются твердость НВ и механические характеристики

каждой поковки, каждая поковка принимается индивидуально.
По механическим характеристикам поковки подразделяются на категории
прочности (КП). После букв KJ1 ставится цифра, соответствующая пределу
текучести металла в кгс/мм². При увеличении диаметра или
толщины поковки требования к пластическим свойствам материала
снижаются. В табл. 1.26 приведены механические характеристики поковок
из углеродистых и легированных сталей по ГОСТ 8479—70 диаметром или
толщиной до 300 мм. Чтобы обеспечить необходимые механические
характеристики поковок, следует выбрать соответствующую марку стали. В
табл. 1.27 приведены данные для поковок диаметром или толщиной до 100
мм.
1.24. Механические характеристики качественной углеродистой конструкционной стали (по ГОСТ 1050—60)
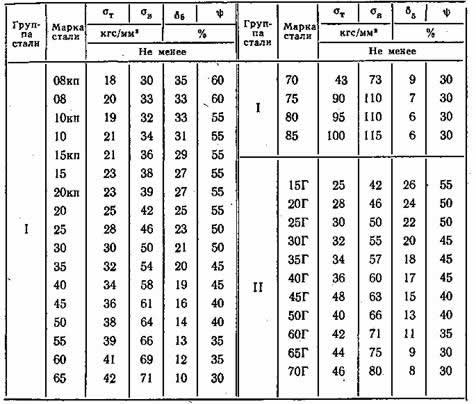
1.25. Цвета маркировки углеродистой качественной конструкционной стали (по ГОСТ 1050—60)

1.26. Механические характеристики поковок из углеродистых и
легированных сталей (по ГОСТ 8479—70) диаметром (толщиной) до 300 мм
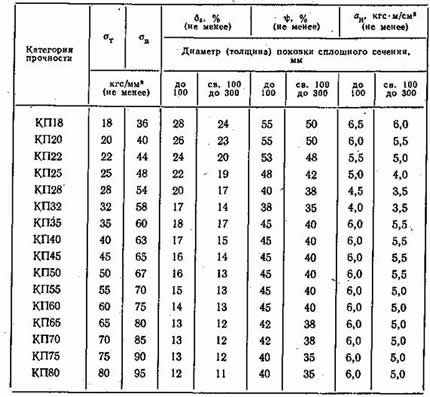
Отливки из углеродистой стали по ГОСТ 977—65 подразделяются на три
группы: группа I — обычного назначения; группа II — ответственного
назначения; группа III — особо ответственного назначения. Отливки
группы I подвергаются наружному осмотру, размеры контролируются,
твердость по Бринелю определяется лишь по требованию заказчика. У
отливок группы II определяются предел текучести и относительное
удлинение. У отливок группы III проверяются значения предела текучести,
относительного удлинения и ударной вязкости. Отливки II и III групп
проверяются по химическому составу. У отливок I группы проверяется лишь
содержание серы и фосфора.
Отливки всех групп по требованию
заказчика проходят дополнительно специальный вид контроля: испытание
гидравлическим давлением, дефектоскопию и пр.
1.27. Рекомендуемые марки стали для поковок диаметром или
толщиной до 100 мм в зависимости от требуемой категории прочности (по
ГОСТ 8479-70)
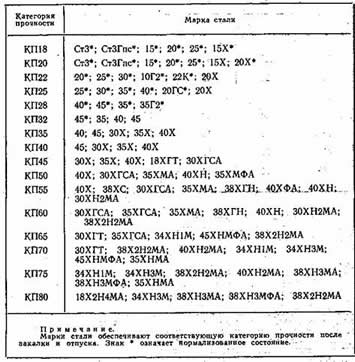
В термически обработанном состоянии отливки из углеродистых сталей
должны удовлетворять требованиям табл. 1.28. Для изготовления деталей
арматуры применяются углеродистые стали от 15-ЛП до 45-ЛП и от 15-ЛIII до 45-ЛП1. Наиболее широко используется сталь марки 25Л-И,
она применяется при давлениях

и температуре

.
Для работы в условиях

и

, когда требуется гарантировать определенные показатели ударной вязкости, применяется сталь марки 25Л-1П.
Легированные стали. Легированные стали перлитного
класса применяются в основном для арматуры, работающей при температуре
не выше 455° G, и для крепежа (табл. 1.29).
Высоколегированные
стали и сплавь согласно ГОСТ 5632—6 L по коррозионной стойкости и
теплостойкости подразделяются на следующие группы:
1) группа I —
коррозионностойкие (нержавеющие) стали, обладающие стойкостью против
электрохимической коррозии (атмосферной, почвенной, щелочной,:
кислотной, солевой, морской и др.);
1.28. Механические характеристики отливок из углеродистых сталей, применяемых для деталей арматуры (по ГОСТ 977—65)
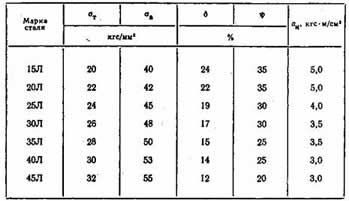
2) группа II — жаростойкие (окалиностойкие) стали и сплавы,
обладающие стойкостью против химического разрушения поверхности в
газовых средах при температурах выше 550° С, работающие в ненагруженном
или слабо нагруженном состоянии;
3) группа III — жаропрочные
стали и сплавы, работающие в нагруженном состоянии при высоких
температурах в течение определенного времени и обладающие при этом
достаточной окалиностойкостью.
К сталям условно отнесены сплавы с содержанием железа более 45%.
Высоколегированные
стали по структурным признакам подразделяются на следующие шесть
классов: мартенситный, мартенсито-ферритный (не менее 5— 10% феррита),
ферритный, аустенито-мартенситный, аустенито-ферритный (феррита более
10%) и аустенитный. Подразделение сплавов: сплавы на железо-никелевой
основе и сплавы на никелевой основе.
Из высоколегированных сталей
в арматуростроении применяются главным образом стали мартенситного,
ферритного и аустенитного классов (табл. 1.30 и 1.31). Стали
аустенитного класса обладают высокими пластическими свойствами,
коррозионностойки, немагнитны.
Механические характеристики отливок из легированных сталей, применяемых в арматуростроении, приведены в табл. 1.32.
В
обозначениях марок сталей буквы означают: А — азот, Б — ниобий, В —
вольфрам, Г — марганец, Д — медь, Е — селен, М — молибден, Н — никель,
Р — бор, С — кремний, Т — титан, Ф — ванадий, Ю — алюминий. Буква А,
обозначающая азот, в конце марки не ставится. В обозначениях марок
сталей цифры указывают среднее содержание (в процентах) элемента, за
буквой обозначения которого цифра стоит. Содержание элементов,
присутствующих в стали в малых количествах (бор, азот, титан), цифрой
не обозначается. Цифры перед буквенным обозначением указывают
содержание углерода в стали в десятых долях процента. Если содержание
углерода не ограничено нижним пределом при верхнем 0,09% и более, цифра
впереди не ставится. При содержании углерода до 0,04% в начале
обозначения марки ставится знак 00, при содержании углерода до 0,08% ~-
знак 0. Название марок сплавов состоит только из буквенных обозначений
элементов, и только после никеля указываются цифры, обозначающие его
среднее содержание в процентах.
1.29. Механические характеристики легированных конструкционных сталей, применяемых для деталей арматуры
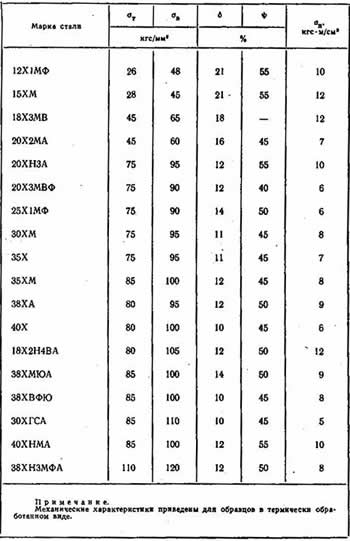
1.30. Коррозионностойкие стали, применяемые для деталей арматуры
Марка стали Назначение Допустимые пределы температур, *Сот до
1X13 Шплинты и стопорные шайбы в арматуре -40 450
из чугуна
2X13 Детали арматуры для воды, нефтепродуктов,
сред слабой агрессивности и детали, подвергающиеся -40 450
атмосферной коррозии
3X13; 4X13 Детали высокой твердости, пружины —40 450
Х17 Детали
арматуры для пищевой и мясомолочной
промышленности, консервных заводов,
спиртоводочного
и дрожжевого производства, азотнокислотных заводов,
работающие в различных средах средней агрессивности —20 300
1Х17Н2 то же, что для стали Х17, но при требованиях
высокой твердости и прочности —70 350
9X18 Детали с высокой твердостью и прочностью
при коррозионной стойкости —40 300
Х14Г14НЗТ Заменитель
стали Х18Н10Т для арматуры, работающей
в средах слабой агрессивности
(органические кислоты
невысоких концентраций и умеренных температур,
соли,
щелочи), для арматуры в пищевой промышленности,
для низкокипящих
сред; детали, подвергающиеся
атмосферной коррозии, свариваемые детали и
детали
из тонкого листа —200 300
Х21Г7АН5 Детали, работающие в условиях глубокого холода,
требующие материал повышенной прочности —253 300
ОХ21Н5Т; 1Х21Н5Т Сварные
детали арматуры для коррозионных сред
химической, пищевой и других
отраслей промышленности;
применяются взамен стали Х18Н10Т —70 300
1Х16Н4Б Высокопрочные штампосварные детали, работающие
в агрессивных средах —50 300
ОХ18Н10Т; Х18Н9Т;
ОХ18Н10Т-ВД;
1Х18Н10Т-ВИ Детали
арматуры для азотной кислоты, пищевых и других
коррозионных сред. При
температурах не более 75° С
сталь Х18Н9Т применима для
нейтрально-сульфатного и
сульфатного щелоков —253 600
Х32Н8; Х32Н8-ВД;
X32H8-III Детали
арматуры для работы в морской воде и
окислительных средах при
требованиях высокой
коррозионной стойкости и повышенной прочности —40 250
Х18Н22В2Т2 Особо напряженные детали судовой арматуры.
Обязательна термообработка с указанием категории прочности — * 350
Х17Н13М2Т;
Х17Н13МЗТ;
ОХ17Н16МЗТ Детали арматуры для кипящей фосфорной, муравьиной,
молочной, уксусной кислот и других' сред повышенной
агрессивности —200 600
Х18Н12С4Т Детали арматуры для концентрированной азотной кислоты — 100 80
ОХ21Н6М2Т Заменитель Х17Н13М2Т для сварных деталей —70 300
ОХ23Н28МЗДЗТ Сварные детали арматуры для серной кислоты различных
концентраций, кроме нефтористой кислоты и других
фтористых соединений 80
ОХ23Н28М2Т Сварные
детали арматуры для горячей фосфорной кислоты
с примесью фтористых
соединений и серной кислоты низкой
концентрации (до 20%) 60
ОООХ21Н16АГ8 Сварные детали для длительной работы в условиях глубокого
холода -253 300
ОХ18Н12Б Детали арматуры для сред высокой агрессивности,
в которых сталь Х18Н10Т не обладает достаточной
коррозионной стойкостью 600
1.31. Жаропрочные стали и сплавы, применяемые для деталей арматуры
1.32. Механические характеристики отливок из легированных и высоколегированных сталей, применяемых для деталей арматуры
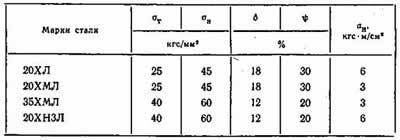
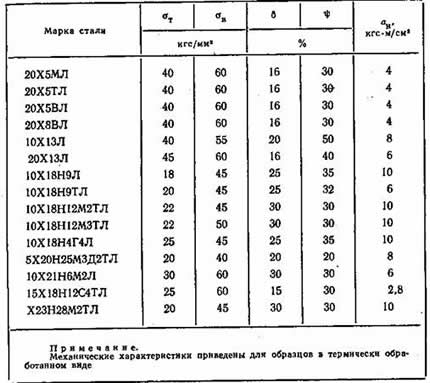
4.3 Цветные металлы и стали Латуни в трубопроводной арматуре применяются для изготовления
уплотнительных колец для воды, ходовых гаек, электропроводящих деталей
приводов. В некоторых случаях из латуни изготовляется также мелкая
пароводяная арматура, когда такая необходимость технически обоснована.
Латунь — пластичный материал, имеет хорошую коррозионную стойкость (для
повышения коррозионной стойкости производится отжиг латуни). С
понижением температуры механические свойства латуни повышаются, поэтому
она успешно применяется для арматуры, работающей при низких
температурах. В табл. 1.33 приведены механические характеристики
латуней, применяемых в арматуростроении. Латуни применяются при
температуре

Для неответственных литых деталей арматуры, работающих при низких
давлениях, применяется кремнистая латунь марки ЛК80-ЗЛ и латунь
свинцовистая марки ЛС59-1Л. Латунь ЛЖМц59-1-1 используется для поковок
шпинделей, ходовых гаек и;в других случаях. Для изготовления
ходовых гаек применяются также латуни марок Л К80-3, ЛМцС58-2-2 и
ЛС59-1. Уплотнительные кольца задвижек и вентилей изготовляются из
латуней марок Л62 (прокат), ЛМцС58-2-2 и ЛК80-ЗЛ (отливки). Латунь
ЛЖМц59-1-1 может применяться для изготовления деталей арматуры,
работающей в условиях низких температур (до —196° С).
Бронза в
арматуростроении применяется для изготовления шпинделей, ходовых гаек,
подшипников, втулок, венцов червячных колес, а также пружин, работающих
в коррозионной среде и электромагнитном поле. Механические
характеристики бронз, применяемых в арматуростроении, приведены в табл.
1.34.
1.33. Механические характеристики латуней, применяемых в арматуростроении
1.34. Механические характеристики бронз, применяемых в арматуростроении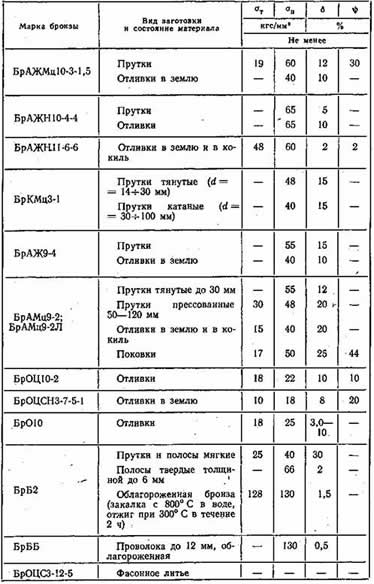
1.35. Механические характеристики отливок, изготовляемых из алюминиевых сплавов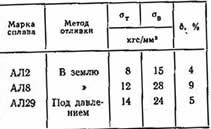
Безоловянная бронза БрАЖМцЮ-3-1,5 применяется для изготовления
шпинделей и ходовых гаек, работающих в широком диапазоне температур (от
—180 до +300° С). Бронза БрАЖН 10-4-4 используется для шпинделей, а
бронза БрАЖН! 1-6-6 — для ходовых гаек, работающих при температуре от
—180 до +350° С. Для изготовления литых деталей, работающих при низких
температурах (до —180° С), применяется безоловянная бронза БрАЖН!
1-6-6Л. Детали, работающие в морской воде, изготовляют из бронзы
БрОЦ10-2.
Алюминиевые сплавы используются в основном для
арматуры, работающей при температурах от —80 до + 100°С. Из сплавов
марок АЛ2 и АЛ8 изготовляется мелкая арматура, краны и детали проводов.
Алюминий марки АО применяется для, изготовления арматуры, работающей на
азотной кислоте. Алюминий марок АО, А и АД1 используется для прокладок,
работающих при температуре от —253 до +100° С. В табл. 1.35 приведены
механические характеристики отливок из алюминиевых сплавов, применяемых
для изготовления деталей арматуры. С повышением температуры прочность
алюминиевых сплавов быстро снижается (например, при 200° С предел
текучести и предел прочности примерно в 1,5 раза меньше, чем при 20° С).
Никель
и никелевые сплавы хорошо противостоят действию коррозионных сред и, в
частности, действию морской воды. Одним из важнейших свойств никеля
является его способность сохранять пластичность при низких
температурах. В интервале температур от +650 до —271° С пластические
свойства никеля не изменяются.
Из никелевых сплавов в
арматуростроении наиболее распространен монель-металл НЖМц28-2,5-1,5
устойчивый против действия морской воды, содержащий никеля 68%, меди
28%, железа 2,5% и марганца 1,5%. Его механические характеристики
приведены в табл. 1.36. Кроме монель-металла в арматуре применяется
никель (ограниченно) следующих марок: HI (99,8%), Н2 (99,6%) и НП-2.
Титановые
сплавы получают все большее применение. Арматура из титановых сплавов
пригодна для работы в коррозионных средах, при низких и повышенных
температурах; она обычно выполняется сваркой. Из титановых сплавов
изготовляются также сильфоны. Титан имеет плотность

,
стоек в атмосферных условиях, в пресной и морской воде, горячих
минеральных маслах, щелочах калия и натрия, пищевых продуктах, в ряде
кислот и других средах. Титан имеет низкие антифрикционные свойства и
склонность к задиранию при трении скольжения, поэтому рабочие
поверхности при трении должны подвергаться соответствующей обработке
или наплавке. В табл. 1.37 приведены механические характеристики
некоторых титановых сплавов.
1.36. Механические характеристики монель-металла НМЖМц28-2,5-1,5
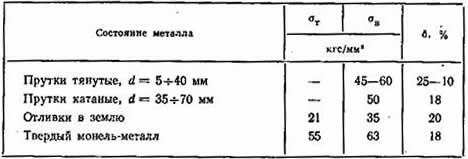
1.37. Механические характеристики некоторых титановых сплавов
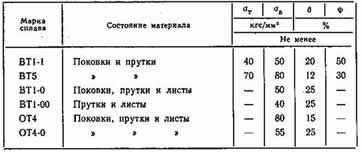
4.4 Неметаллические конструкционные материалы В арматуростроении возрастает количество конструкций, в которых
используются различные неметаллические материалы, хотя удельный вес их
еще в общем остается небольшим.
Пластмассы используются для
изготовления деталей или для облицовки (футерования) внутренних
поверхностей корпусных деталей, непосредственно соприкасающцхся с
коррозионными средами.
В и k,H пласт представляет собой твердую
негорючую пластмассу, получаемую путем термической пластификации
поливинилхлоридных смол. Обладает высокой химической стойкостью против
действия многих агрессивных сред — кислот, щелочей и их растворов. Из
винипласта изготовляются вентили, краны, клапаны и др. Он используется
также как футеровочный материал. Применяется для рабочей среды с
температурой до 40—60° С.
Фторопласт-4 по химической стойкости
превосходит все химически стойкие материалы, включая золото и платину.
Разрушается лишь под действием расплавленных щелочных металлов и
элементарного фтора. Не смачивается водой и не набухает, по внешнему
виду напоминает парафин. Имеет низкий коэффициент трения и обладает
очень высокими диэлектрическими характеристиками. Применяется для
работы при температуре от —195 до +250° С. Ползучесть этого материала
зависит от удельного давления и температуры. Фторопласт-4 используется
для изготовления деталей кранов, вентилей, труб, сильфонов, мембран,
прокладок, сальниковых набивок и различных деталей электроаппаратуры.
Фторопласт-3
применяется для температур до 70° С, выпускается в виде плит толщиной
1—8мм, трубок и шнура, используется также для покрытия шероховатых
металлических поверхностей, предварительно нагретых до температуры 275°
С.
Полиэтилен используется как коррозионностойкий материал для
изготовления и футерования арматуры, изготовления отдельных деталей,
уплотнительных колец, прокладок.
1.38. Механические характеристики некоторых неметаллических материалов и пластмасс, применяемых для изготовления арматуры.
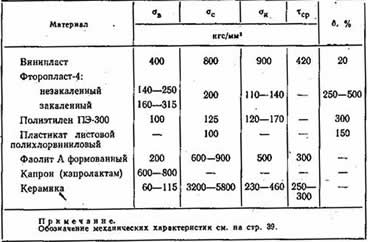
1.39. Сплавы повышенной стойкости, применяемые для наплавки уплотнительных поверхностей арматуры
Марка электрода Область применения
ВЗК (подслой толщиной Арматура на высокие и сверхвысокие параметры,
2— 4 мм из стали Х18Н10) для коррозионных и
агрессивных сред; трущиеся и
уплотнительные поверхности при температуре
от
— 196 до +600° С
НЦ-2; ЦН-3
Арматура на высокие и сверхвысокие параметры при
температуре от -100 до +570°С
Сормайт № 1 ЦН-12; ЦН-12М Уплотнительные поверхности задвижек
УОНИ 13/М1-БК До температуры среды 200° С
Фаолит — кислотоупорная пластмасса, изготовляемая на основе
бакелитовой смолы, применяется как для футерования арматуры, работающей
при температуре среды до 120° С, так и для изготовления некоторых
конструкций вентилей и кранов.
Капрон, пропилен, нейлон, текстолит, древеснослоистые пластики и другие пластмассы имеют в арматуре ограниченное применение.
Стекло,
фарфор, диабаз плавленый, кислотоупорная керамика и графитные материалы
успешно применяются для изготовления труб и некоторых деталей
трубопроводной арматуры химических произ